Burrs during li-ion battery electrode slitting and punching create serious quality risks. These tiny protrusions interfere with proper electrode contact, directly reducing battery capacity by 5-15% in severe cases.
More critically, burrs become safety hazards - laboratory tests show even 20μm protrusions can puncture separators, leading to thermal runaway. The financial impact compounds through multiple channels: higher internal resistance cuts cycle life by 30%, while burr-related scrap rates typically add 3-8% to production costs.
For reliable slitting performance, manufacturers need durable tungsten carbide slitter knives specifically engineered for electrode materials. Shen Gong's li-ion battery electrode slitting knives demonstrate longer lifespan than standard blades in continuous production. The secret lies in three innovations: 1) Ultra-fine grain carbide substrates resistant to micro-chipping, 2) Proprietary TiCN coatings reducing copper/aluminum adhesion by 40%, and 3) μm-level edge finishing that prevents initial burr formation.
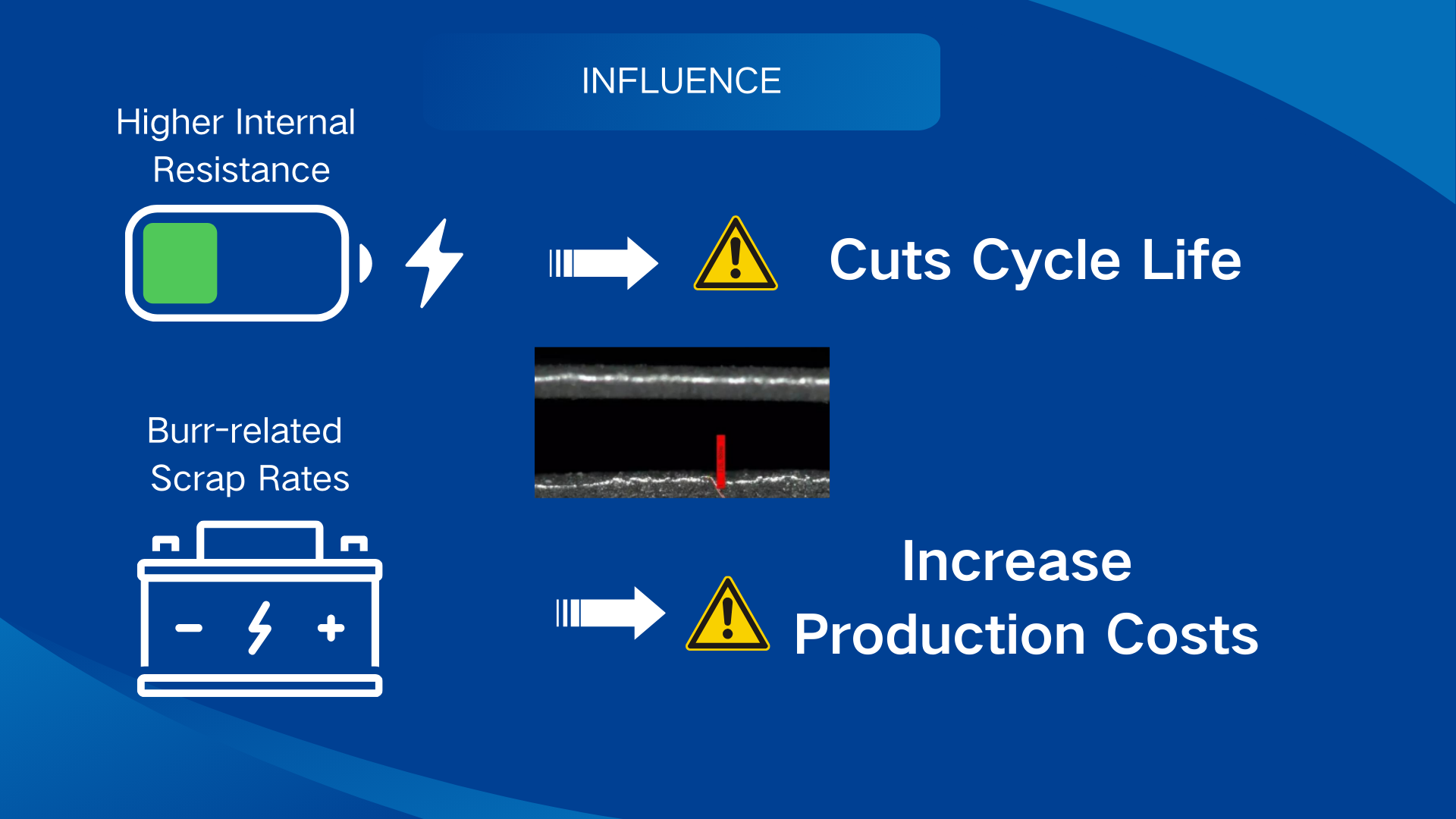
Operational best practices further enhance results:
• Implement blade rotation every 8 production hours
• Maintain 0.15-0.3mm cutting depth relative to electrode thickness
• Use laser measurement tools for weekly wear inspection
For new energy vehicle battery lines, our matched upper/lower blade sets achieve <15μm cut tolerances consistently. Case studies show reduction in burr-related defects after switching to Shen Gong's system. Remember - while premium slitting blades cost 20-30% more initially, they prevent exponentially higher downstream losses from scrap and battery failures.
If you are experiencing burr issues in electrode slitting, please consult the ShenGong technical team: howard@scshengong.com
Post time: Apr-22-2025